Specialist Advice on What is Porosity in Welding and Just How to Resolve It
Wiki Article
The Science Behind Porosity: A Comprehensive Guide for Welders and Fabricators
Understanding the complex mechanisms behind porosity in welding is critical for welders and makers aiming for flawless craftsmanship. From the make-up of the base products to the complexities of the welding process itself, a plethora of variables conspire to either intensify or relieve the visibility of porosity.Comprehending Porosity in Welding
FIRST SENTENCE:
Assessment of porosity in welding reveals essential insights into the stability and quality of the weld joint. Porosity, defined by the existence of cavities or voids within the weld steel, is an usual problem in welding procedures. These voids, if not effectively resolved, can compromise the architectural integrity and mechanical residential properties of the weld, bring about potential failures in the ended up product.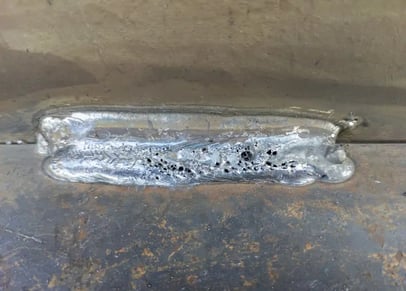
To find and quantify porosity, non-destructive testing approaches such as ultrasonic testing or X-ray inspection are commonly utilized. These methods allow for the recognition of internal issues without endangering the honesty of the weld. By assessing the size, shape, and distribution of porosity within a weld, welders can make informed decisions to improve their welding procedures and accomplish sounder weld joints.
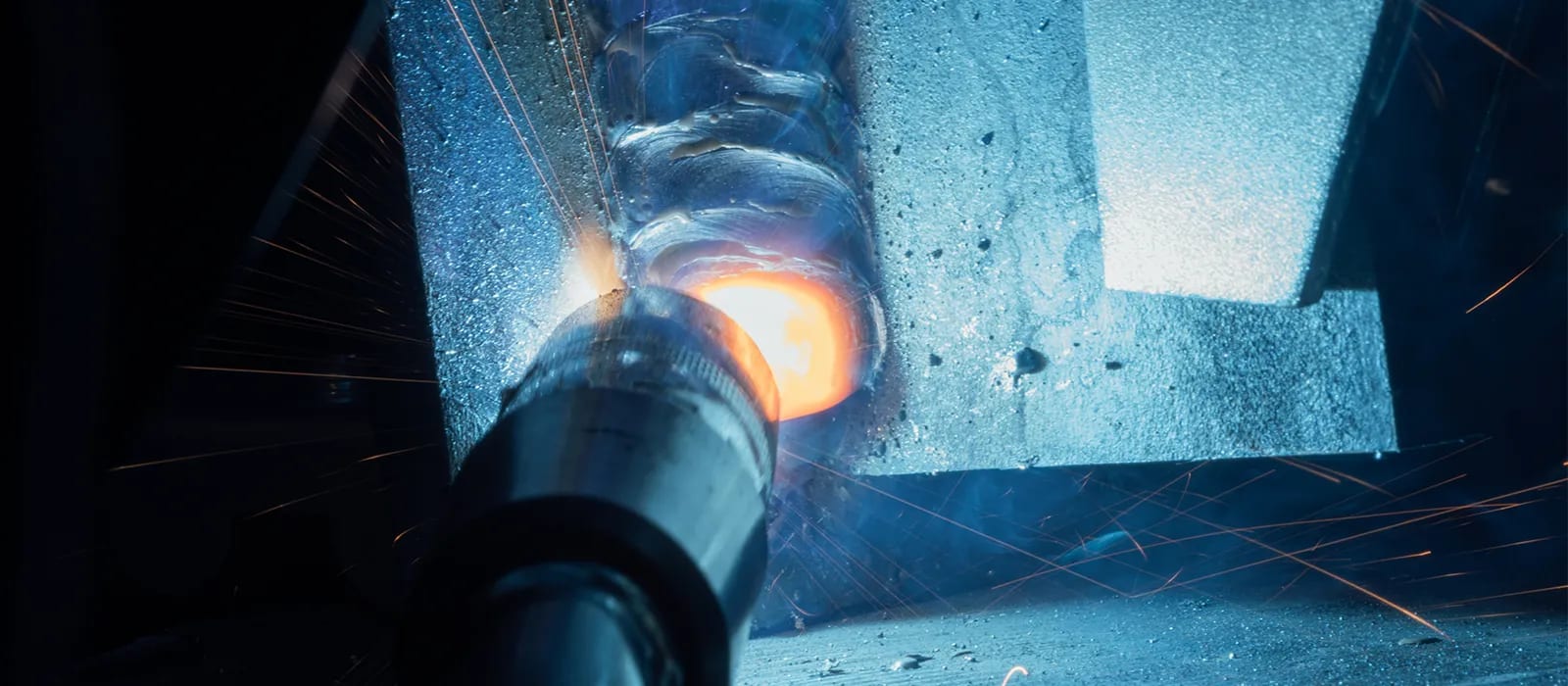
Variables Influencing Porosity Formation
The event of porosity in welding is affected by a myriad of variables, ranging from gas protecting effectiveness to the details of welding criterion settings. One vital element adding to porosity development is insufficient gas securing. When the protecting gas, typically argon or CO2, is not efficiently covering the weld swimming pool, climatic gases like oxygen and nitrogen can pollute the molten metal, causing porosity. Furthermore, the sanitation of the base materials plays a considerable role. Contaminants such as rust, oil, or wetness can evaporate during welding, creating gas pockets within the weld. Welding criteria, consisting of voltage, present, travel speed, and electrode type, likewise effect porosity development. Making use of inappropriate settings can click here for info create excessive spatter or warm input, which in turn can result in porosity. The welding technique employed, such as gas steel arc welding (GMAW) or shielded metal arc welding (SMAW), can influence porosity development due to variants in warmth distribution and gas insurance coverage. Understanding and regulating these elements are necessary for decreasing porosity in welding operations.Impacts of Porosity on Weld High Quality
Porosity development substantially compromises the architectural honesty and mechanical buildings of welded joints. When porosity exists in a weld, it develops spaces or cavities within the material, decreasing the general stamina of the joint. These gaps serve as stress focus points, making the weld more prone to splitting and failing under tons. The existence of porosity additionally compromises the weld's resistance to corrosion, as the caught air or gases within the spaces can respond with the surrounding atmosphere, resulting in check here degradation gradually. Furthermore, porosity can prevent the weld's ability to stand up to pressure or impact, more jeopardizing the general high quality and reliability of the welded structure. In essential applications such as aerospace, auto, or architectural buildings, where security and toughness are critical, the detrimental impacts of porosity on weld high quality can have severe effects, stressing the importance of reducing porosity with appropriate welding techniques and treatments.Methods to Decrease Porosity
Additionally, making use of the appropriate welding parameters, such as the appropriate voltage, present, and travel speed, is important in avoiding porosity. Preserving a consistent arc size and angle during welding likewise assists decrease the possibility of porosity.
Utilizing the ideal welding method, such as back-stepping or using a weaving motion, can likewise help distribute heat uniformly and decrease the opportunities of porosity formation. By carrying out these techniques, welders can successfully lessen porosity and produce premium bonded joints.
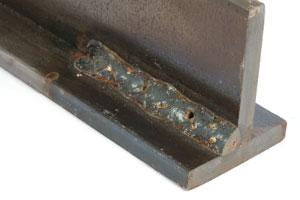
Advanced Solutions for Porosity Control
Applying innovative modern technologies and innovative approaches plays an essential my blog role in accomplishing superior control over porosity in welding processes. One sophisticated remedy is the use of advanced gas combinations. Securing gases like helium or a combination of argon and hydrogen can help in reducing porosity by providing far better arc stability and improved gas protection. Furthermore, employing advanced welding methods such as pulsed MIG welding or changed environment welding can also help reduce porosity concerns.Another innovative remedy entails using sophisticated welding equipment. Utilizing equipment with built-in attributes like waveform control and innovative power sources can boost weld quality and lower porosity risks. Moreover, the implementation of automated welding systems with accurate control over specifications can considerably reduce porosity issues.
Moreover, including advanced tracking and assessment modern technologies such as real-time X-ray imaging or automated ultrasonic testing can aid in identifying porosity early in the welding procedure, permitting for immediate rehabilitative activities. Overall, incorporating these sophisticated options can considerably boost porosity control and boost the total high quality of bonded parts.
Verdict
In conclusion, comprehending the scientific research behind porosity in welding is important for welders and producers to create premium welds - What is Porosity. Advanced services for porosity control can further enhance the welding process and ensure a strong and reputable weld.Report this wiki page